Despite several challenges ahead, the need for insulation for renovations and new builds continues to be pronounced.
After all, the purpose of a home is to protect homeowners from the elements and that means — at a minimum staying warm during cold Canadian winters.
Of course, like all construction, that doesn’t mean everything’s coming up roses. “The industry is in a little bit of a crisis,” says Gino Allegro, Canadian Sales Manager at Johns Manville. Allegro, who had just finished chairing an Ottawa meeting of the Board of Directors of NAIMA (North American Insulation Manufacturers Association) Canada, the association for manufacturers of glass fibre, rock wool, and slag wool insulation, says the current national housing crisis is top of mind across members.
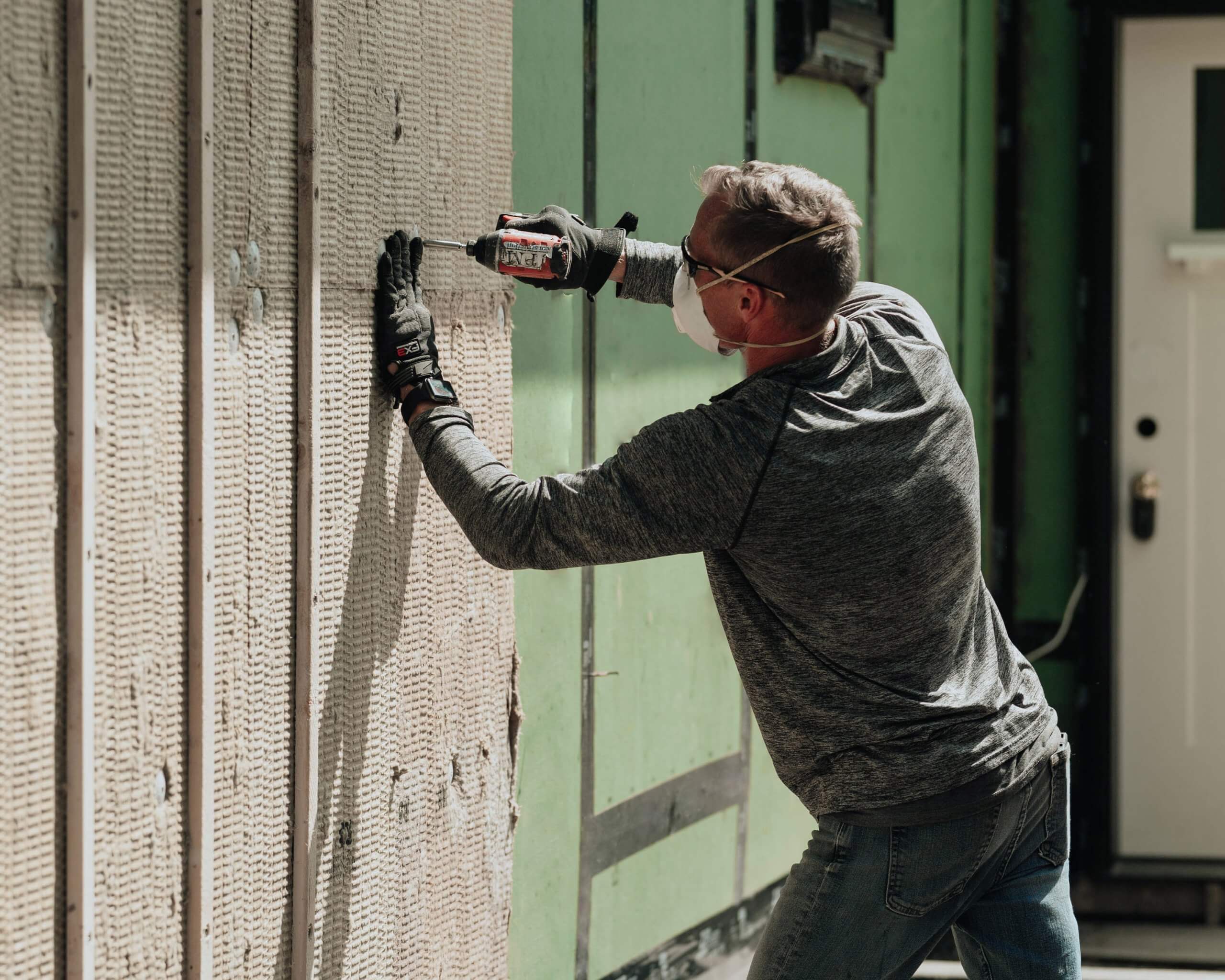
Photo courtesy of Rockwool
“There are a lot of people coming into Canada, and while they may be staying with family or sponsors today, those are temporary. They are going to need real accommodations, and there’s going to be a huge pent-up demand in the next 10 years. The federal government is working on this.”
In a 2022 report, the Canada Mortgage and Housing Corporation noted that housing supply has not responded to demand for the past 20 years, especially in large urban areas, leading to the housing affordability challenge we see today. Add to that the lack of skilled labour and the crisis becomes even more clear.
But for manufacturers, distributors, and installers of insulation, that pent-up demand combined with growing environmental expectations means a steady requirement for insulation products. While there will be ebbs and flows, “the insulation industry is going to be in robust demand for the next 10 years,” Allegro says.
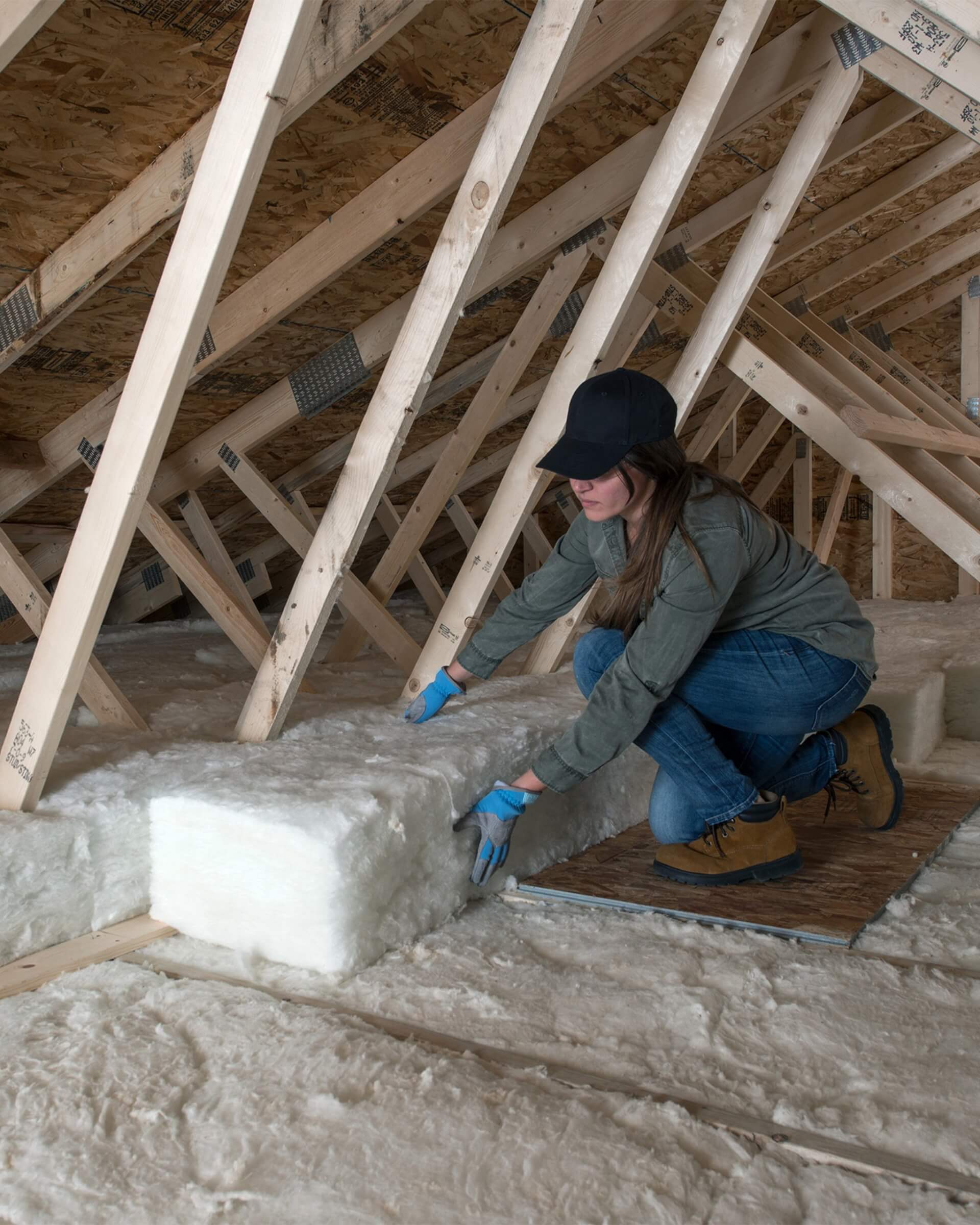
Photo courtesy of Johns Manville
Net-zero goals
By creating a thermal barrier that reduces heat transfer, insulation is, of course, a vital part of reducing the energy required to heat and cool spaces — and as a result lowering energy bills and reducing greenhouse gas (GHG) emissions.
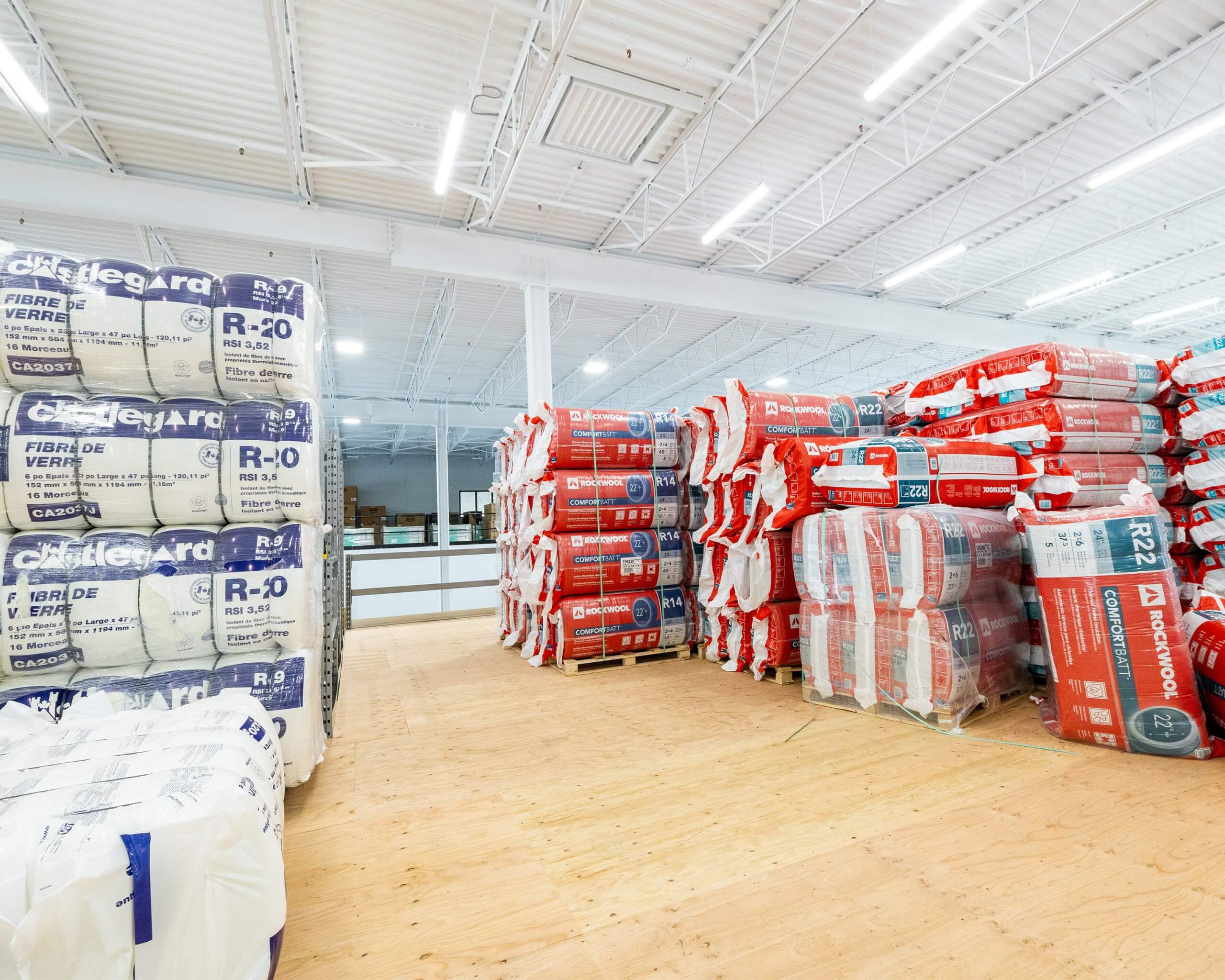
Photo courtesy of Adams Building Supply
As a nation, Canada has a goal of achieving net-zero emissions by the year 2050. Recognizing the impact that homes and buildings have on GHG emissions, building codes have already started to create a path towards achieving net-zero standards by 2030. The federal codes, creating a net-zero-ready standard, are being harmonized with provincial codes at different rates across the country. Still, the demand for higher performance in energy efficiency is high in every province or territory.
“The ‘built environment’ accounts for 13% of greenhouse gas emissions in Canada —both building codes and consumer preferences are driving towards net-zero-ready as an increasing standard for residential construction across Canada. Continuous insulation is a necessity in net-zero design. Also, looking for construction methodologies that minimize concrete and steel, such as more use of wood or mass timber framing into taller (above 4 storey) structures,” says Martha Swinn, Canadian sales leader at DuPont.

Photo courtesy of Johns Manville
The thermal efficiency of insulation will be a major requirement but contractors must remember how insulation functions as part of a building system in reducing energy consumption.
“Obviously with more stringent codes, more insulation will be needed in order for structures to become more thermally efficient, but also there will be a need for greater air tightness,” says Brent Belanger, Architectural Services Manager at CertainTeed Canada.
Codes alone aren’t driving the green building movement, so Belanger and others are seeing a lot of concern around carbon footprints from consumers. To that end, householders (and homeowners to be) have evolved in their expectations around environmental friendliness.
“Initially people were thinking of green buildings just in terms of thermal efficiency, but now that has evolved,” Belanger says. “It’s not just the building performance, but what’s going into the building products and the making of them.”
To that end, with its own commitment to a net-zero 2050 target, Belanger says CertainTeed Canada invests significant resources into the lifecycle analysis of its insulation products, and the publishing of EPDs, environmental product declarations that provide environmental information about the product from creation to disposal and aids in comparison with other solutions.
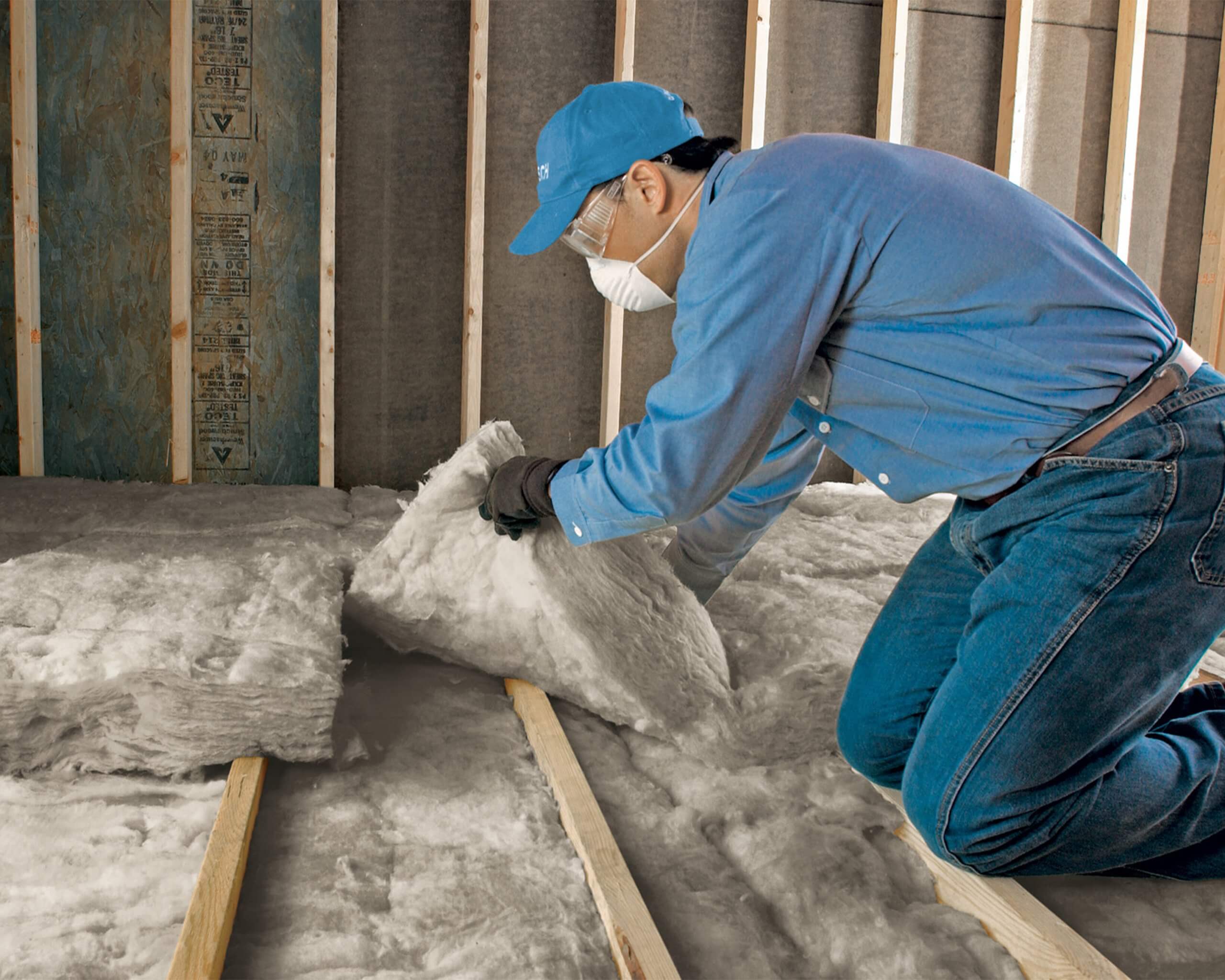
Photo courtesy of CertainTeed Canada
It appears everyone is doing their part. According to NAIMA, its members in Canada and the U.S. used more than 3.5 billion lbs. of recycled glass and slag in the production of their residential, commercial, industrial, and air-handling thermal and acoustical insulation in 2022.
The association says this reduces demand for virgin resources and diverts glass and slag from landfills. Since the industry’s recycling program began in 1992, NAIMA says its members’ plants have diverted more than 100.5 billion lbs. of recycled materials from the waste stream.
Manufacturer innovations are making a difference in efforts to reduce Global Warming Potential (GWP). For example, by reformulating the production of Styrofoam for its XPS (Extruded Polystyrene) insulation products, DuPont was able to reduce GWP by 93% since 2019.
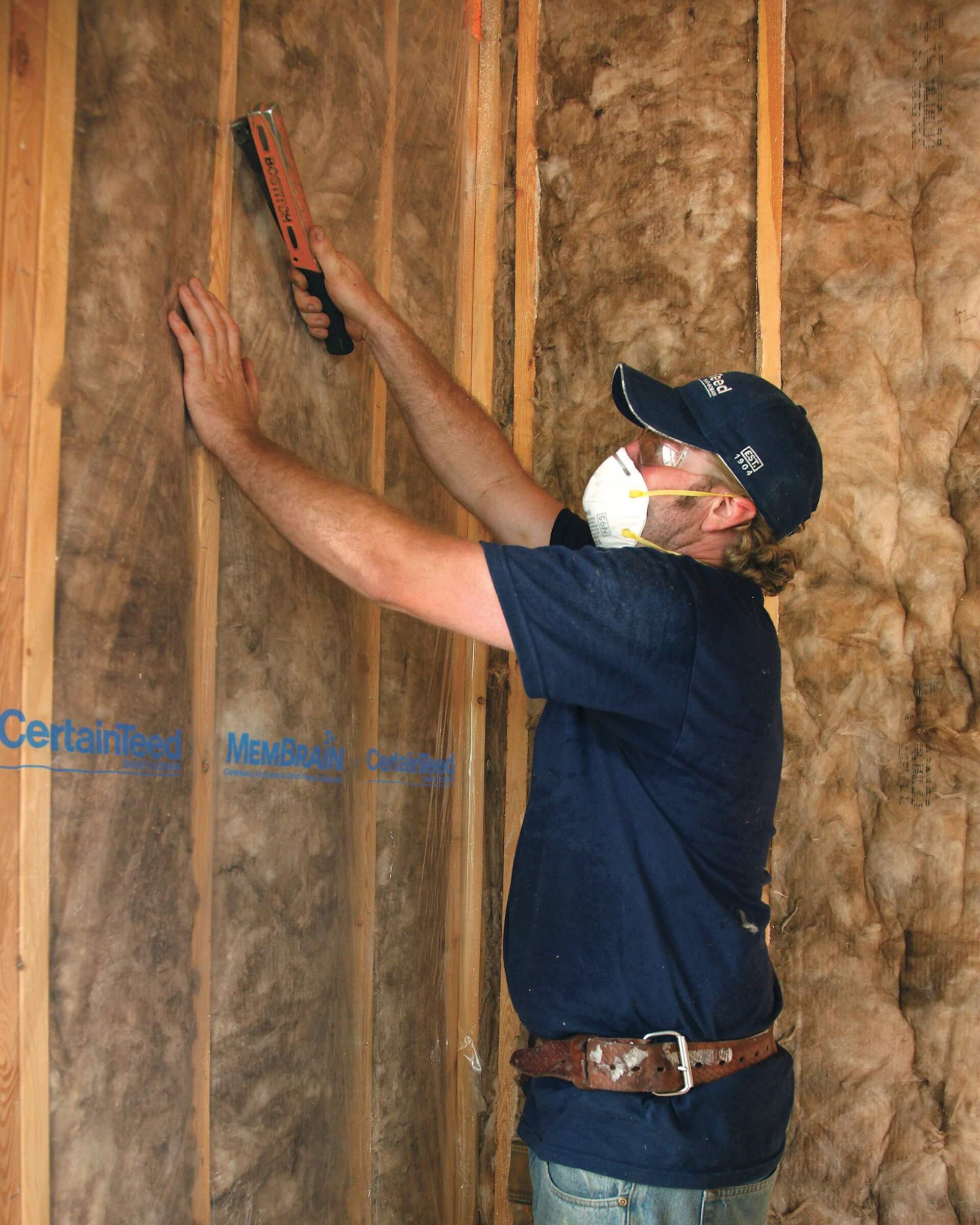
Photo courtesy of CertainTeed Canada
Moving forward, “Innovation will focus on building envelope solutions, including continuous insulation and full weatherization systems, to support resiliency — temperature, rain, wind, and fire,” Swinn says. “And also, to support alternate construction methodologies in off-site space.”
Swinn says contractors can expect building science experts like Dupont to continue their longtime advocacy around energy efficiency through next-generation sustainable, climate-conscious products.
It’s important to note that achieving net-zero homes is going to require more than adding additional glass fibre batts to the attic or in the walls — after all, only so much can fit between 2x6 studs. As R-value requirements climb to meet thermal efficiency expectations the trend will be to move outside the house using rigid insulation boards, says Mike Goyette, National Sales Director at Rockwool North America.
As codes get closer to net-zero requirements, Belanger says he expects under-slab insulation to be mandated in addition to insulated sheathing and increases in attic insulation. “You’re looking at every part of the building; every facet of the building envelope is going to have more insulation.”
According to Goyette, a major trend impacting the insulation market is the increase in renovations and retrofits — primarily to meet growing energy performance demands.
“There is a lot of new insulation going into old buildings,” he says. “It might be, for example, going from say 6” to 24” in the attic. They are really loading it up.”
“Some people are even willing to rip down the outside of their home and then rebrick to improve performance. The rebuild and retrofit market is growing.”
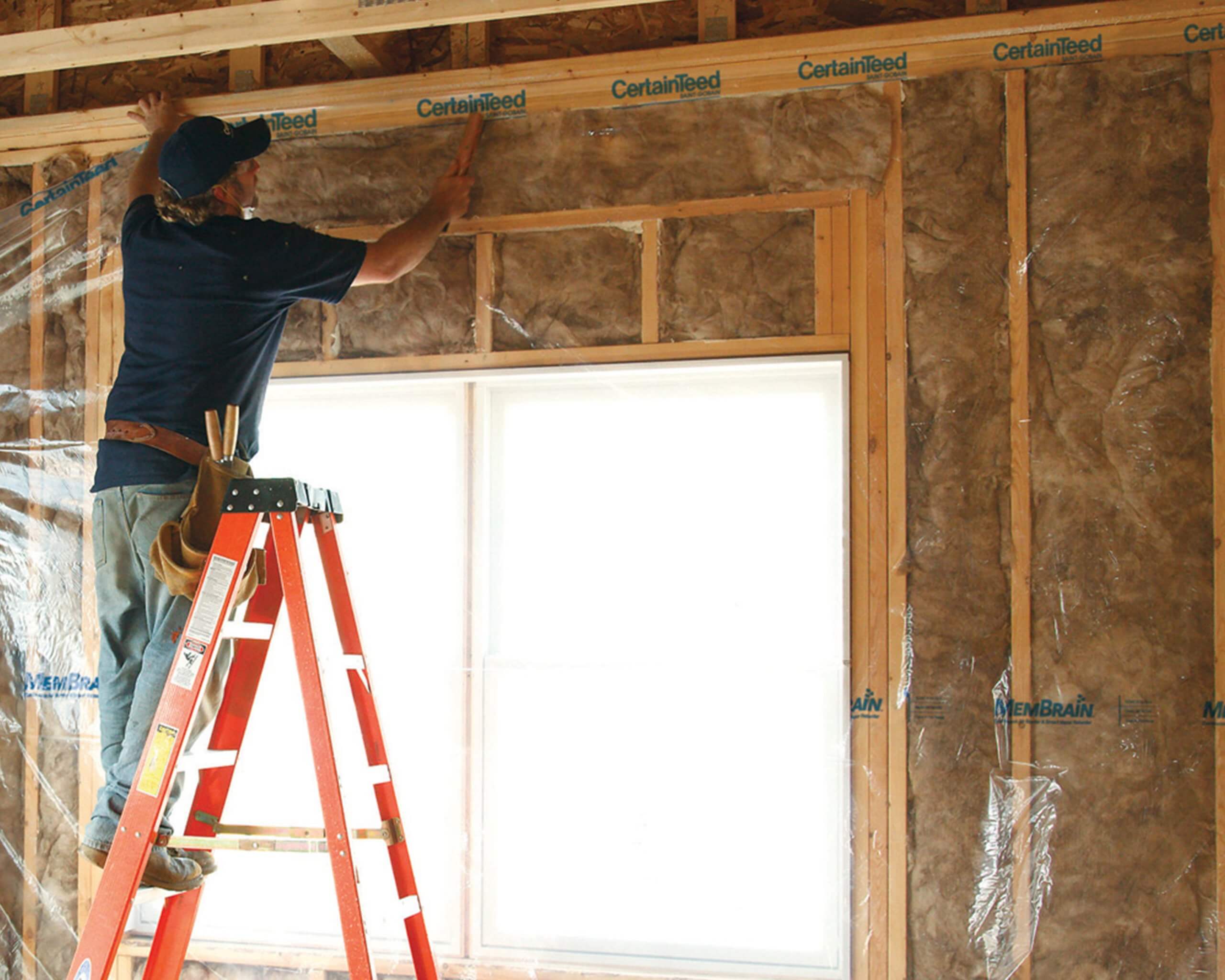
Photo courtesy of CertainTeed Canada
Comfortable and quiet
While protecting the environment is a top concern, comfort is king when it comes to why people add insulation to their homes.
While properly insulated homes see reduced heat transfer, staying warm in the winter and cool in the summer months, they also improve indoor air quality, according to NAIMA. They can also, Goyette notes, reduce noise.
“There’s cold, yes, but there’s also acoustics,” he says. “If you insulate with acoustical products you aren’t going to hear that toilet flush from the bathroom or the teenager cranking up the music in the other room.”
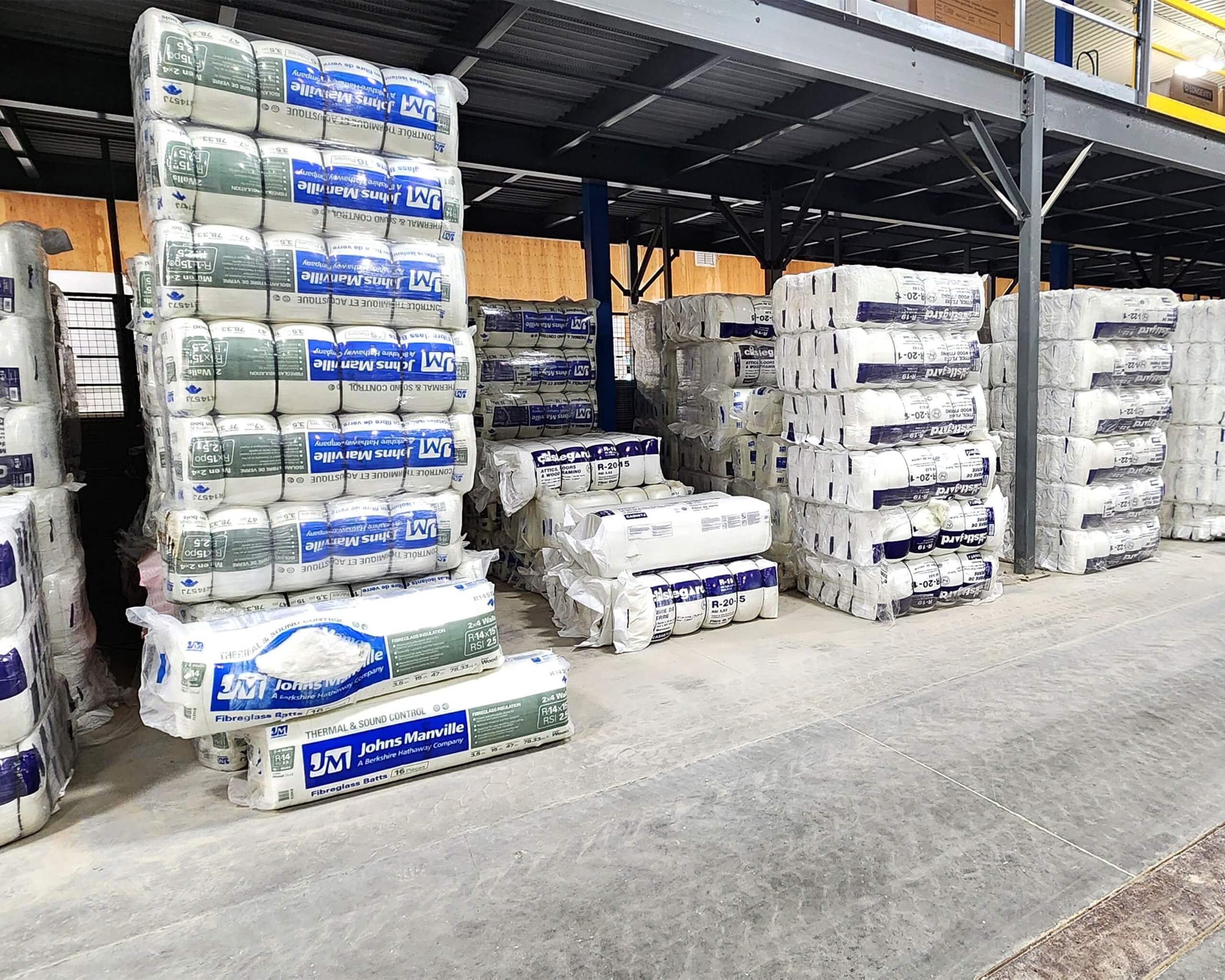
Photo courtesy of Adams Building Supply
As a result of the 2020 pandemic and more people working from home, finding a way to control acoustics has become more important to consumers, he says. Despite offices reopening and hybrid work conditions, the trend towards sound-dampening insulation hasn’t gone away.
“I think the trend continues, in part, because more people are putting in basement apartments in their homes,” he says, adding that this too is a result of Canada’s housing cost challenges. “If you talk to anyone who works the lumber desk at your local Castle, you’ll see that the basement apartment trend is what’s keeping them busy.”
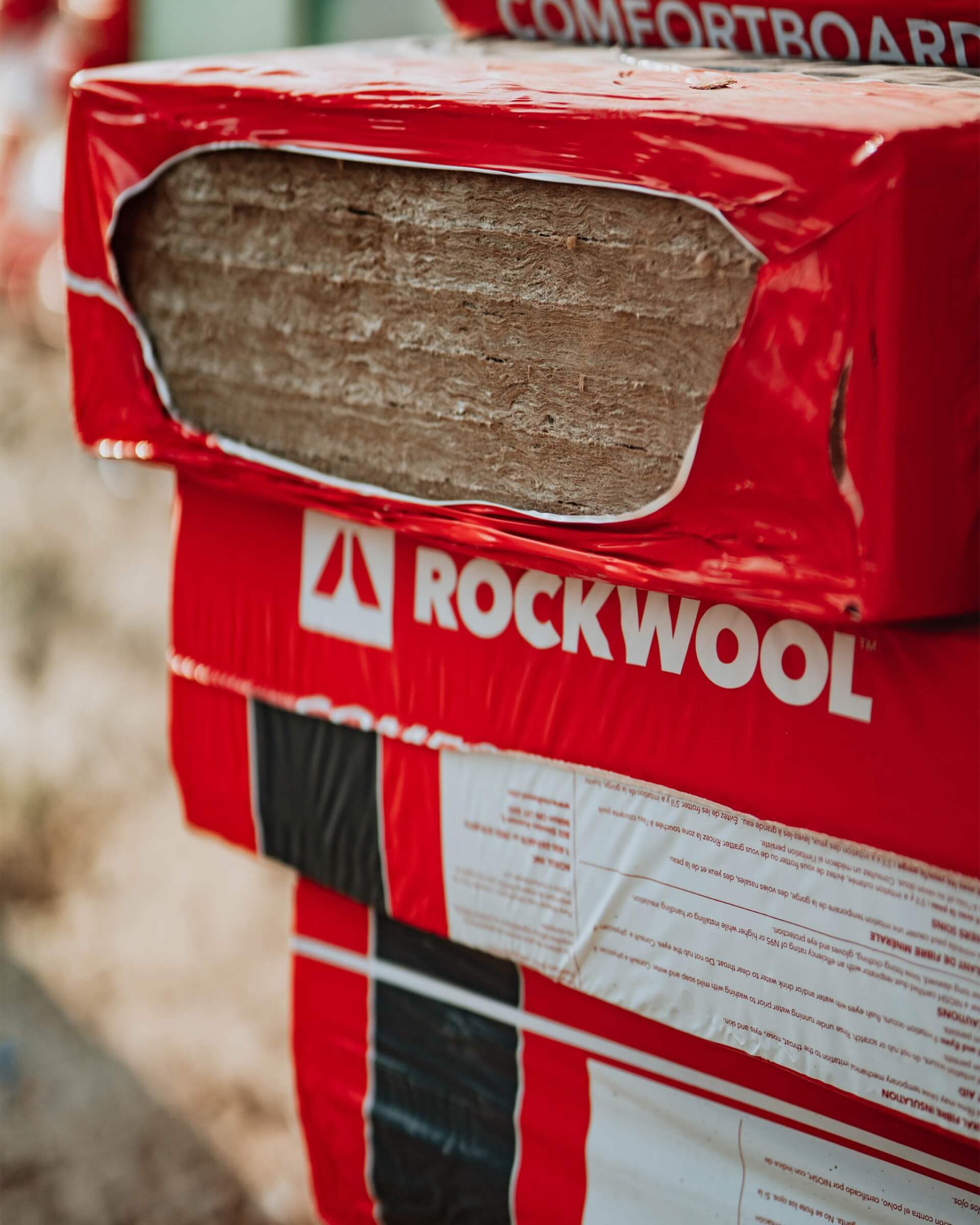
Photo courtesy of Rockwool
Safety is a concern, and with it the movement towards non-combustible insulation materials is huge, says Goyette. It’s a sentiment echoed by Belanger, who notes that insulation is very helpful in improving the fire resistance of a home.
“Performance, whether its fire, thermal or acoustic, is critical on insulation, and unfortunately, being behind a wall it suffers from being out of sight, out of mind,” Belanger notes.
Allegro reminds contractors and homeowners that there’s only one cost-effective shot to get it right.
“Whether it’s an addition or renovation project, or new construction, you only get one shot at this before the drywall is put on,” he says. “It’s not the most expensive part of the house, but it’ll provide that added level of comfort.”
“One shot while the studs are bare, and you can do it easily. If you’re doing any kind of construction, more on insulation may cost a little bit more, but can make a huge difference in comfort and energy efficiency.” —
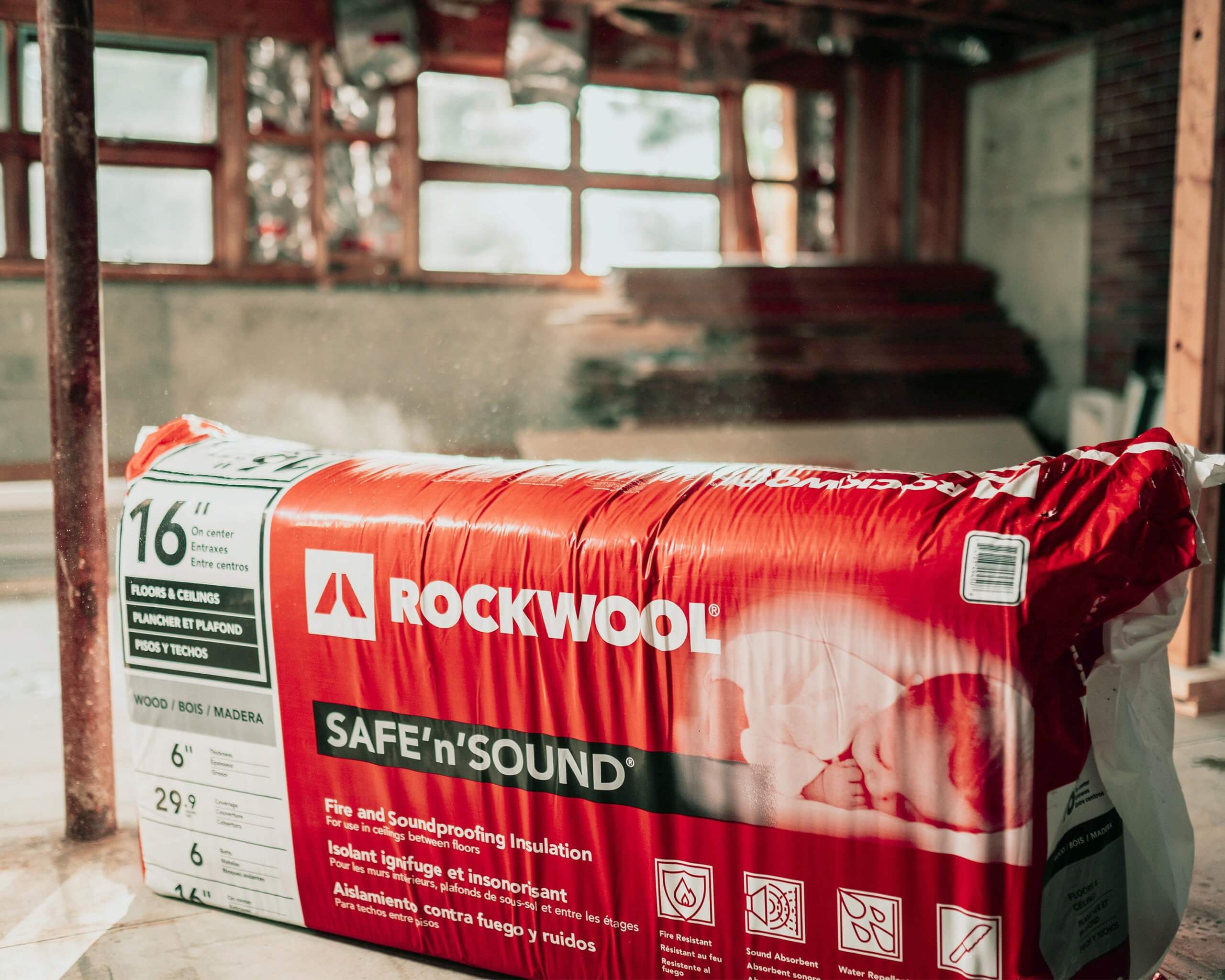
Photo courtesy of Rockwool